MIKO
Welding companion for small scale-metal workshops
How might we introduce collaborative robots into small scale workshops to increase safety among workers?
Vision for collaborative robotics | Small-scale or large-scale?
The way collaborative robotics are seen today is solely humans and robots working next to each other without the robots harming the human. However, working collaboratively is more about communication, support and helping each other. This does not happen in large-scale production facilities because the tasks are monotonous, and the robots do not need to be reprogrammed that often. With this set up, robots stay as machines working behind cages. Bringing industrial robotics from large-scale to small-scale production facilities opens a room for true collaboration between humans and robots with a high level of interaction. In the small scale workshop, the robot can become a co-worker rather than a machine working next to you.
Miko is a professional welding robot for small-scale metal workshops. It is designed to work in a close collaboration with the welder. Small-scale metal workshops compete with larger production facilities by being able to offer flexibility. This requires them to have an agile process and equipment that is efficient and easy to set up. Miko aims to bring automation into the small-scale metal workshops. With the help of the teaching tool Link, Miko is fast to set up and does not require any prior skills in programming. With Miko in your team, you can avoid health risks caused by exposure to harmful fumes, strenuous positions and UV-light. Miko finishes the job while the welder is planning for the next one, increasing efficiency and safety in small-scale metal workshops.
2017 | 8 weeks | Teamwork with Jakob Dawod & Jon Sommarström
in collaboration with ABB Corporate Research
with user feedback from Allmek Svets
IDEA 2016 Silver
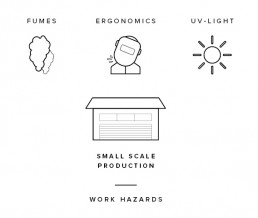
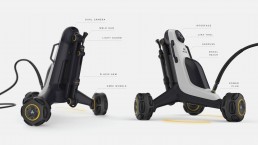
Mobile to adapt momentary needs
Traditional industrial weld robots are one-off solutions where perform one task repeatedly in a fixed position. It became obvious during our field research that in small-scale workshops there is a need for flexible automation. Welder’s tasks vary from day to day and that their workstations are transformed according to the needs of the job. Because of this, the solution had to be flexible to be able to help wherever needed; and provide a wide reach to cover variety of different tasks.
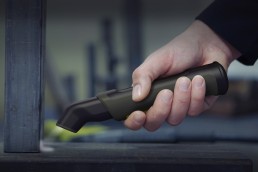
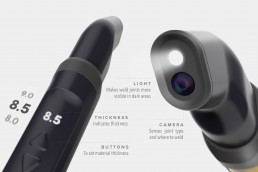
Easy set-up
Small-scale workshops having 5-20 employees, cannot afford hiring specialist to program welding robots. This hinted that the product had to be easy to operate so that any welder could use it without prior knowledge of programming. Link is the main interaction tool between the welder and the robot. The welder shows the weld path to Miko by simply going over the edges with Link. With the help of indoor triangulation system and image recognition, Miko knows where to apply the weld. Link makes it possible to operate Miko in a more natural way, similar to how welding is done today. Because of this, Link’s semantics are inspired by the traditional weld guns.
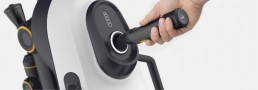
Activation & Feeling in control
Miko is activated by docking Link into the interface. This way, we aimed to give a feeling of control to the welder.
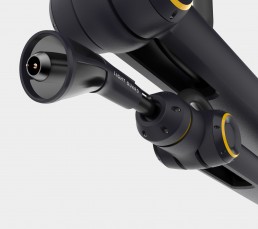
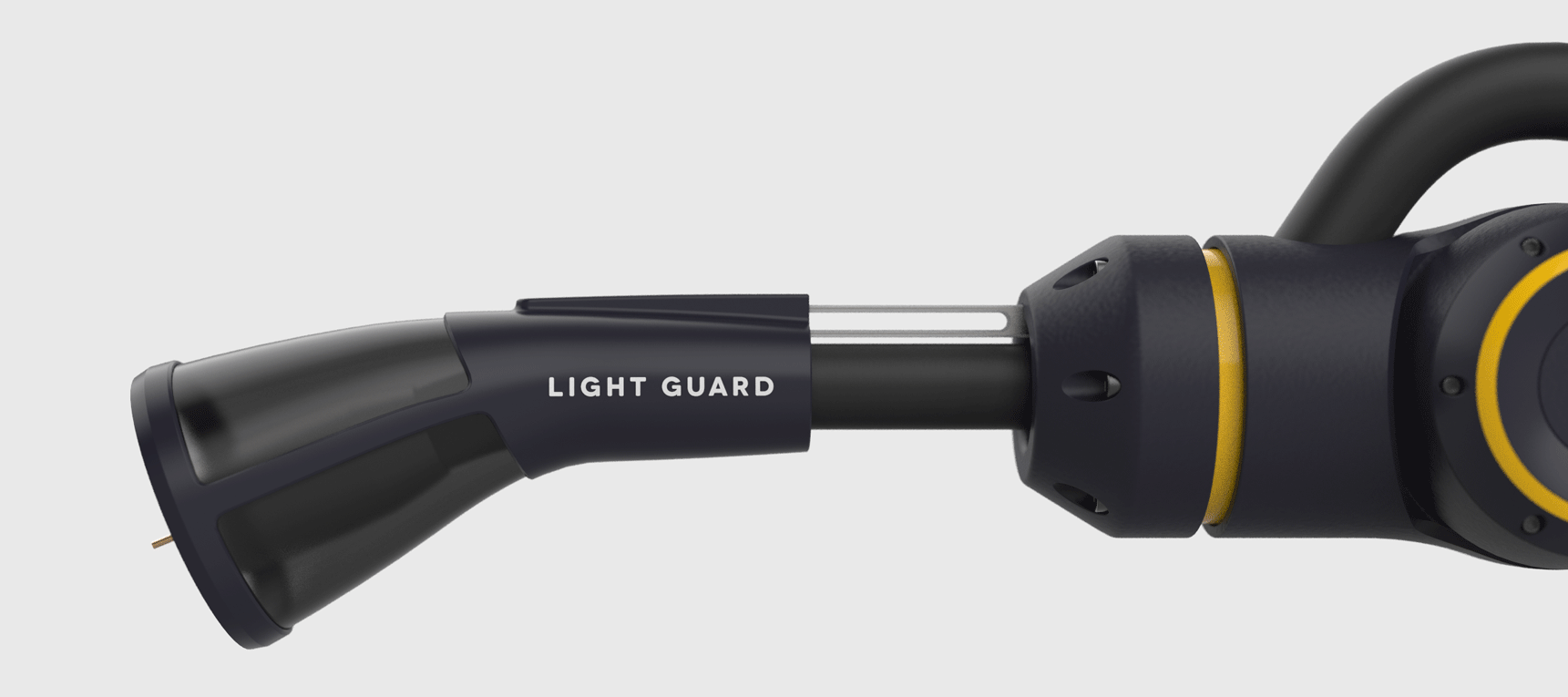
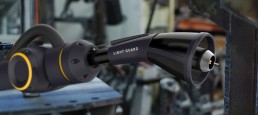
Light Guard
When welding you need to take into considerations your colleges around you. Being exposed to the light from the arc can cause eye damage. The adaptive Light Guard makes MIKO into a safe assistant in the workshop reducing the risk of coworkers being flashed by the arc from the weld gun. It extends or retracts depending on ease of access to the weld area.
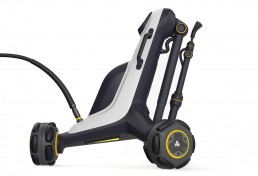
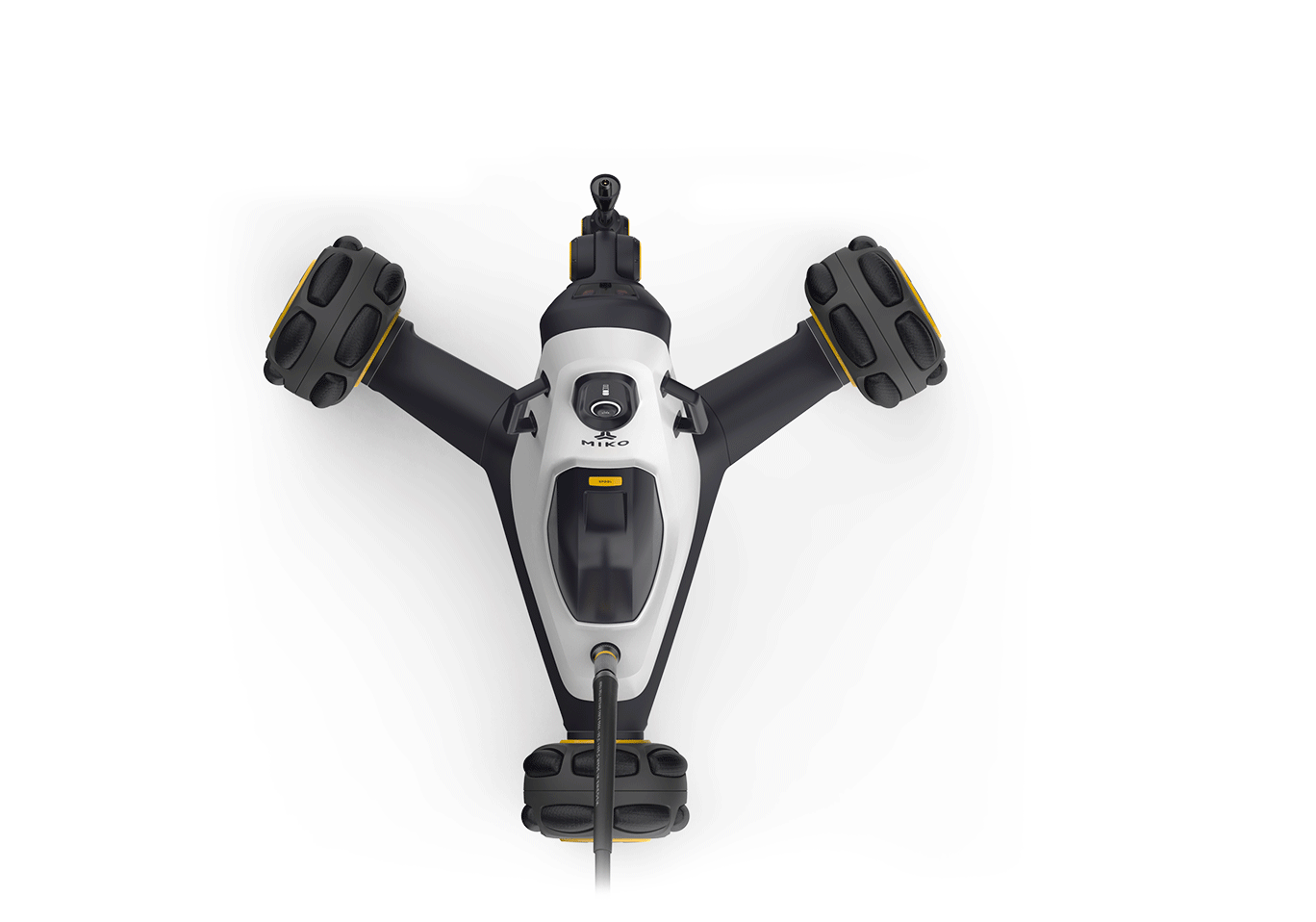
Approachable
Today cage free industrial robots are safe to be around. They work at low speeds and stop when a person gets too close. However, delivering the feeling of safety and being safe is two different concepts. For a collaborative robot working next to humans, it becomes important to deliver a feeling of safety. Based on these insights, we worked on the semantics of Miko and tried to balance friendly character and performance driven workshop product look. To give predictability to its actions, Miko shows its direction of movements with projected lights on the ground.
PROCESS
5 days Sprint
I got familiar with using sprint for product design projects during my time at Designit. Since this project was quite short, we decided to kick off with a sprint week to get it going quickly. At the end of 5 days, we created a low-fidelity scenario movie and archetype options to see users immediate reactions and make a decision accordingly. With the 1:1 scale low fidelity model, we were able to test reach with respect to sizes of workpieces in small-scale metal workshops.
Process Video
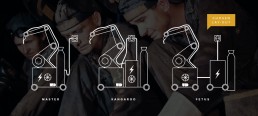
Archetypes
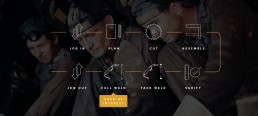
Workflow
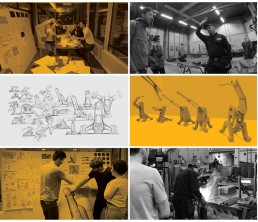
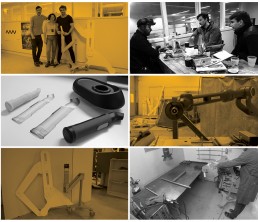
Highlights
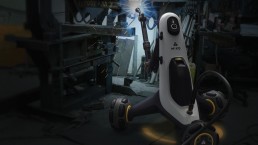